品質方針
お客様の利益に貢献するために、品質の高い商品を提供する。
目標
お客様からのクレームを一番に考え、不良品をお客様に届けない事を
スローガンとして満足して頂ける製品作りをします。
品質管理部
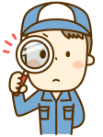
ノークレーム
-
生産管理
品質管理部と製造部の連携により、材料の仕入から梱包までの生産工程を細分化し、役割を明確にする事により、トラブルや不具合が生じた時の対応を迅速に行えるシステムを実現しております。
生産管理システムは、常に変化します。
現状の業務に対しマンネリ化を無くす為、行動効率案、クレーム対策案などを提示し、良い商品を生産し、お客様からの納期を守る事を日々、考えて行動しております。 -
工程管理
工程毎に品質管理部は必ず検査を行います。
図面との細かなズレや、思い込みといったミスを未然に防止させ、商品の取り扱いまで指定をし、キズやダコン、変色や錆を防ぐ対応をし、社内で不良品を必ずストップさせる事で、各工程に与えられた検査項目及び納期を守るを、営業部と連携活動をしております。 -
納期管理
お客様に頂いた納期を必ず守る為、品質管理部は製造部に対し、各機械毎に加工予定表を作成しており、希望納期と照合しています。
納期の変化に対応しやすい様に、材料の供給状態は確保し、予定表の更新はリアルタイムで行い、お客様の最短納期を実現すべき体制を整えております。
製造部
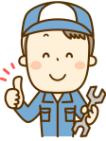
技術向上
-
高精度 - High accuracy -
最新の機械を導入し、径の場合±0.01にて安定した加工を実現させています。長さの場合、材料導入機により2度出しを行い、ある程度の長尺加工を実現させています。市販品の工具では、精度を維持が困難な場合でも、職人により手作業にて工具を作成し難切削にも対応しています。長手NC制御サブスピンドル付で、両側エンド加工はもちろんの事、一台の機械で処理する事により、キズやダコンを最小限にし外観にも注意しています。
-
高品質 - High quality -
お客様の御要望に満足して頂ける製品作りをする為、可能な限り努力を、惜しみません。
当社から、クレームを出させない為にどうしたら良いかを、追求し続けます。
あらゆる、検査器具を有し、その状況に適した器具を使用し、寸法の変化を捉え、お客様の御要望に満足して頂ける製品作りをしております。
検査器具保有例
精度
ミクロンマイクロメータ ±0.001
直進式ブレードマイクロメータ ±0.001
グローブマイクロメータ ±0.01
三点式内側マイクロメータ ±0.001
キャリパー形内側マイクロメータ ±0.001
穴ピッチ用オフセットノギス ±0.01
デジマチックデプスゲージ ±0.01
ダイヤルキャリパーゲージ ±0.01 など -
高効率化 - Highly effective -
過去に加工を行った場合、誰が段取を行ったとしても同じやり方で作業が出来る様にプランニングシート(加工工程、切削条件、ツールのセットアップ、加工時間など)にて管理し、作業工程の見直しや、段取替の効率化、加工時間短縮などの材料として活躍しており、リピート品の対応にも早く対応しております。
生産管理体制-1
-
検査項目
お客様より頂いた図面を元に、寸法や指示のある箇所にNoを設定し、各部署毎の、加工や検査の統一した見解を目的にて、重要な項目です。
-
材料
自社加工品の材料調達から行い、材料の変動には敏感に対応し、コスト意識からスタート致します。
納入時、歪みや、カット引きキズ(引抜材加工にてキリ粉や不純物が付着しそのままの状態にてついてしまうキズの事)等の検査を行い、材料の安定供給に努めております。 -
プランニングシート
製造部が、図面を元に工具の選定を行い、使用品目を一枚のシートに記入していき、プログラム作成の下準備を行います。
機械の段取替当日に、に進行する事と、他の職人が同じ作業手順にて行える為で、細かな点まで記録を残す事により、次回からの加工を迅速かつ、注意点を考慮しながら、プランニングシートを作成しております。 -
量産前検査
自社加工品の材料調達から行い、材料の変動には敏感に対応し、コスト意識からスタート致します。
納入時、歪みや、カット引きキズ(引抜材加工にてキリ粉や不純物が付着しそのままの状態にてついてしまうキズの事)等の検査を行い、材料の安定供給に努めております。 -
工程検査
量産加工に入り、抜取検査を行います。
当社独自で採用している、商品別検査表にて時間を決め、検査項目のNo箇所を定期的に検査を行い、加工時に発生する摩耗や、ドリルや刃先の損傷具合までチェックを行います。 -
洗浄
最終検査終了後、商品に応じた洗浄作業を行います。
非鉄金属系にて洗浄剤を使い分け、お客様がすぐに御使用可能な状態を意識し、特に袋穴加工の奥に残ったキリ粉を除去し、洗浄時に発生しやすいキズやダコンといった事を防止させ、良い商品をお届けする下準備を整えております。 -
梱包
洗浄作業後、梱包を行います。
納品状況により、梱包形態は異なりますが、商品が輸送中の衝撃や、商品を陳列する事により、お客様が取り出しやすい様に心懸け、安心と共にお客さまにお届け致します。
生産管理体制-2(マルトクネットワーク)
-
材料調達
お客様より頂いた図面を元に、寸法や指示のある箇所にNoを設定し、各部署毎の、加工や検査の統一した見解を目的にて、重要な項目です。
-
第一工程
旋盤加工製作図面等に、注意点を記載し間違いが起こりやすい箇所や、注意箇所にマーキングを施し、打ち合わせを行います。加工サンプル及びゲージ類の貸出をし、加工後当社品質管理部にて、ロット数に応じ抜取検査を実施し、次工程に移行します。
第一工程-1
タレパン加工第二工程
フライス加工割加工やキー溝加工が主な加工です。相手物やゲージ類を使い検査します。チャック類のキズやダコンには特に注意を促しす。
二次工程以降の検査では、前工程の検査は基本検査対象外になりますが、上記内容の外観検査は行い、次工程に移行します。第一工程-2
バリ取り加工第三工程
ネジ切加工ネジ径を計測し、ゲージ類にて通り、止まりに収まるかを検査します。目視等にて前工程には無かったキズ等を確認し、次工程に以降します。
第一工程-3
曲げ加工第四工程
穴加工デジマチックキャリパーやピンゲージ等を用いて計測します。前工程にてネジ部に穴加工をする際、再度、検査を行います。垂直に穴が加工されているか、内径部の表面が荒れていないか、図面の指示をに対し適切に加工されているかを確認します。
-
溶接加工
板金加工に挽物加工品を付ける作業にて、図面指示通りにされているか、均等に溶接加工が施されているかを冶具等を用いて検査を行い、鋼板が歪んでいないか定盤にて、スコヤー、シクネスゲージ等にて検査を行います。
-
バフ加工
表面に細かなキズ等を無くし、次工程の表面処理を仕上り良くする為の工程です。溶接箇所がバフにて隙間が生じていないか、均等にバフ加工が施されているか目視にて検査を行い、緩衝材等用いて次工程に移動させます。
-
表面処理
メッキ工程でのラック掛けの位置や取扱方法など、現場にて直接、製品を用いて説明します。メッキ加工の色ムラや変色、生地部が残っていないかを目視にて検査をおこないます。
-
組立
複数の部品を組み合わせ、効率良く確実に作業が進む様に、各種専用冶具を製作し、組立工程表に基づき完成まで仕上げていきます。
-
梱包
納品状況により梱包形態は異なりますが、輸送中の衝撃等には細心の注意を払い、商品を整列する事により、お客様が取り出しやすい様に心掛け、安心と共にお客さまにお届け致します。